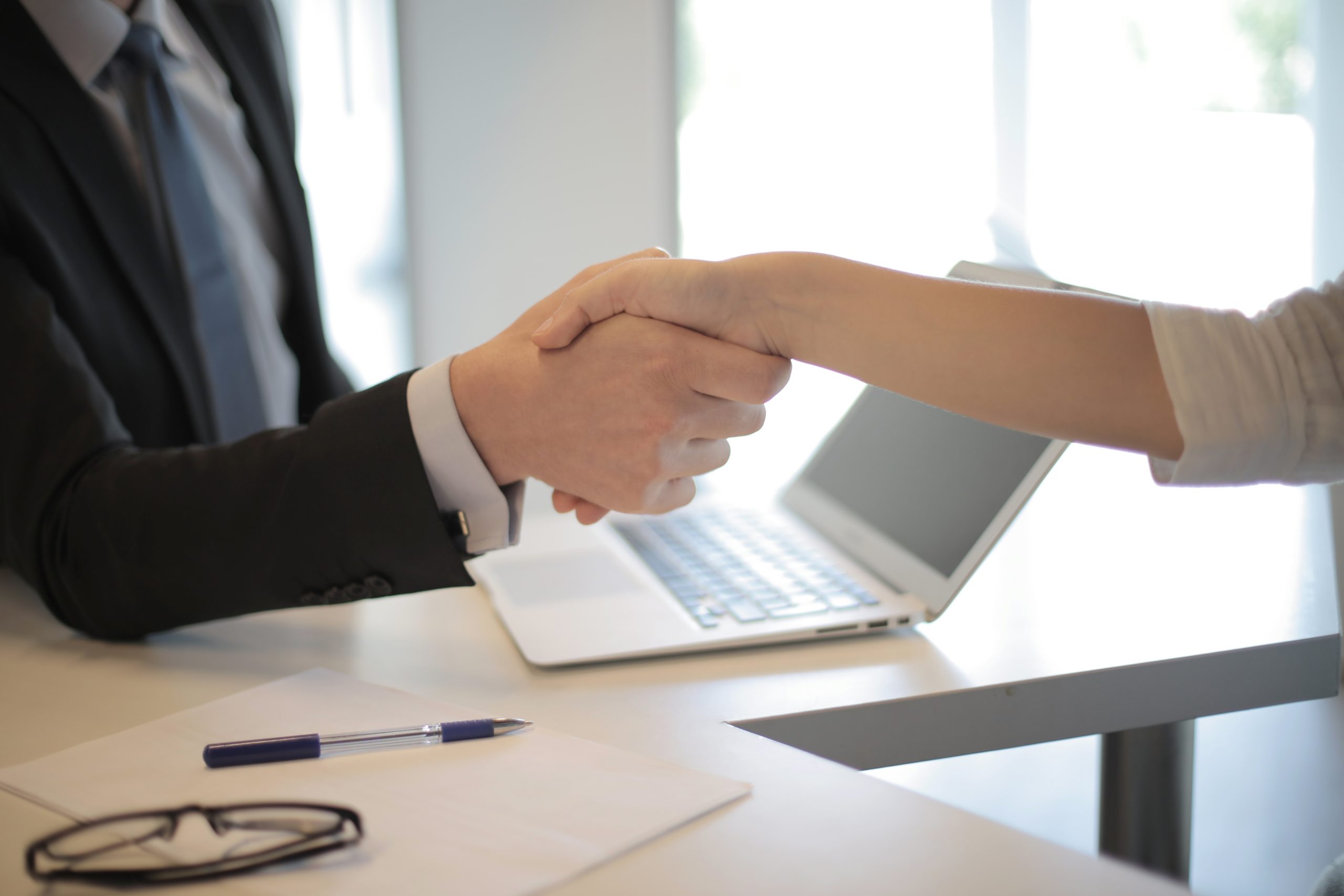
In simple business situations life is easy for cost calculation. There is a simple process, following a single axis. Think of a baker for example. He knows how much of each ingredient he needs to prepare his bread, knows the price, and knows how much rent he must pay per month. But most businesses are not that straightforward. Here is a quick guide to how to properly start costing and controlling in a company.
First thing you need to know: what is the process flow in the company? What is required to produce your end product, what are the steps it has to go through, when does every component have to get in, how is production planned, etc. You need to be able to put into what we will call a “resource flow chart” every single step on the road from raw material and human labour to collecting payments. You get this done? Great, you can go to the next step.
Now starts the part where you get to understand your data flow.
Here you are to go over your resource flow chart again but looking at it from a data entry perspective. Who needs what document, at what time, who fills it in, how and where is the data stored, who has to validate, etc.? You should end up with a “data flow chart” that creates a layer above the resource flow chart, giving you a perfect and complete view of your activity from a data point of view. This step is critical because it is what will help you find the numbers you need to make your calculations and identify bottlenecks and issues.
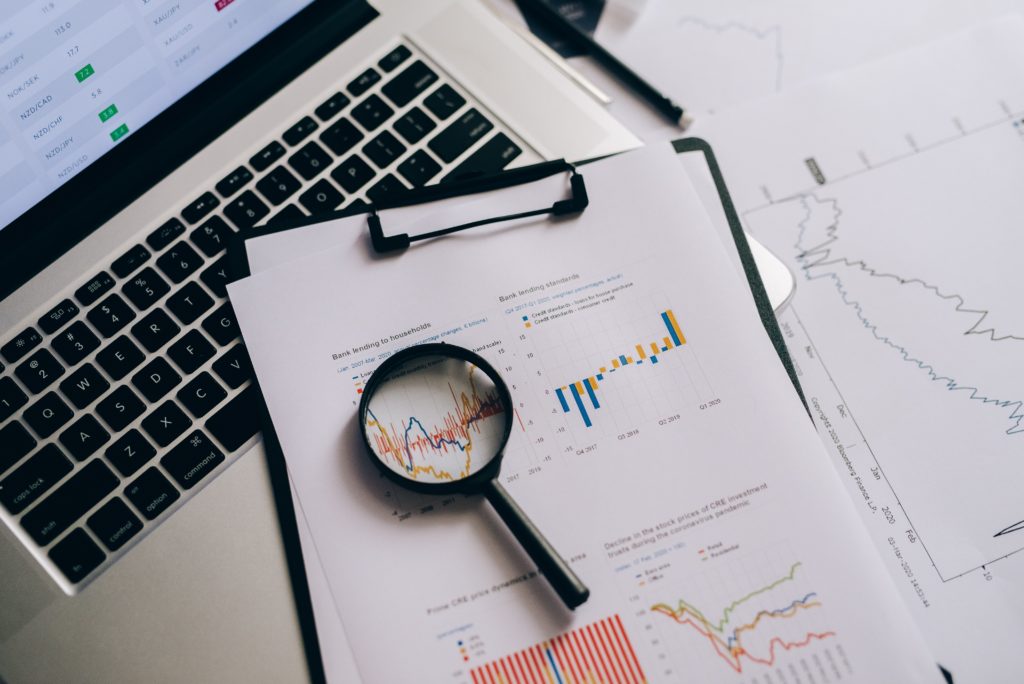
The important aspect of these two first steps doesn’t only lay in being able to find who you need to ask questions when something doesn’t fit, but it is what will give you a true understanding of the company’s functioning at its core. Without this understanding, you won’t be able to put the essential relations between the numbers in accounting and what causes these costs, therefore making it impossible to correctly analyse where you can try to cut costs.
Once these two steps have been done, things get easy. You can associate costs (or the percentage of them that you found statistically) to whatever you want to calculate its cost from, and you can go into calculating ratios and net margins.
Time is precious, maybe, but it is worth investing in the process. Would you rather have your car fixed with the right piece or with duct tape? If you choose for the right piece, you might grunt about having to pay more, but you accept it because you want your car to work and be safe. Do the same with your time.